摘要
化工行业的快速发展促进了社会经济的进步,同时也带来了安全风险的增加。化工安全生产风险点分析与管理是如何保障从业人员生命安全、企业稳健发展的重要措施。本文将从四个方面对化工安全生产风险点分析与管理进行深入阐述,从而提升化工行业安全生产水平。
正文
一、风险点分类
化工企业的安全风险点能够分为两大类,即固有风险点与非固有风险点。固有风险点是由化工过程本身的安全隐患所带来的风险,如高压、高温、腐蚀性化学品等;非固有风险点则是由人为操作、管理不当、装修等因素引起的危险。针对这两大类风险点,我们需要提供具体的分析与管理方案。
(1)固有风险点分析
固有风险点位于生产过程中,是产生化学反应所必须的条件,例如高温、高压等。在化工生产中,这些固有风险点不可避免地存在,然而我们却可以采取措施来规避其带来的安全风险。
巴洛仕集团专业化工厂拆除、危化品处置,危废处理、污泥减量处理、固废处理、土壤修复、化工清洗、化工设备回收等方面可以发挥重要作用。这类企业可以帮助化工厂进行危险品管理和储存,减少储存时的安全风险,并从事风险点分析和管理方面的工作,为企业安全生产提供最佳的保障。
(2)非固有风险点分析
工人的操作行为以及管理不当、装修等因素都会导致非固有安全风险点的产生。例如,操作人员不正确使用个人防护用品、用完后不及时更换等操作上的问题,以及管理人员缺乏对制度、法律、条例制定的意识等管理上的问题。这些问题都会给化工企业的生产活动带来安全风险。
因此,针对这些非固有安全风险点,化工企业需要在日常操作中建立各种制度和规章制度,如在操作流程中制定符合规范的安全程序、定期安排安全会议等等。同时,我们也可以参考国家相关法规制定相关管理条例,对操作人员和管理人员进行培训,以加强对操作规程和安全知识的掌握,降低人为事故的风险。
二、风险防控措施
针对不同类型的风险点,我们需要采取不同的防控措施。例如,我们可以通过改变工艺路线,使用更安全的原材料,来降低固有风险点的产生,同时也可以定期开展安全检查,及时发现安全隐患,进行预测,采取相应的措施,防止事故发生。
同时,我们还可以在企业内设置安全科,对全企业进行安全培训,建立“3S”安全管理制度,即严格的操作规程、充足的人员安全保障和有效的应急措施。这样一来,能够从源头上减少化学品泄漏等事件,提升化工企业的安全生产水平。
三、风险点评价标准
风险点评价标准是针对风险点进行评估的系统方法。评价标准应该以化工安全生产法规为指导,以化工生产及其产生的安全风险为依据。在实际操作中,我们可以通过分析历史事故信息、生产设计文件、废物排放、受污染区域作为因素。根据这些因素进行选择,选择相似企业的一般情况,之后按照风险分级评估标准进行评估。
四、风险点应急预案与演练
万一安全事故发生,应急预案和演练的重要性显得尤为重要。因此我们应制定详细的应急预案,安排专业人员负责应急处置,并准备充足的应急物资。同时,在非紧急情况下,也要进行业务演练,以确保员工对应急预案的执行情况熟悉,并随时准备做好机会应对各种情况的准备工作。
结论
化工安全生产风险点分析与管理是确保化工企业安全生产的重要保障措施。固有风险点和非固有风险点是两类不同的风险。化工企业应该依照评价标准在风险点中逐一进行评估,制定健全的风险控制方案和应急预案,确保全员有充足的安全技能和应对能力。同时,与外部专业化工团队合作,如巴洛仕集团专业化工厂拆除、危化品处置、危废处理、污泥减量处理、固废处理、土壤修复、化工清洗、化工设备回收,也是化工企业提高安全生产水平的重要步骤。
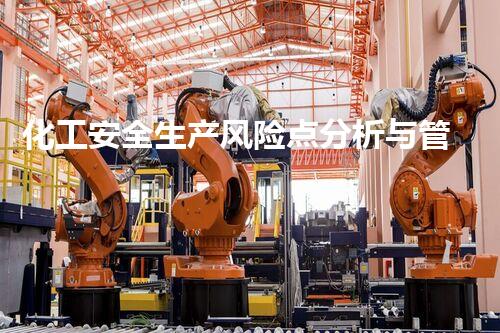