摘要:
鲁西化工是一家实力雄厚的化工企业,为了防范未来的安全隐患,我们可以从历史案例中汲取教训。本文将从四个方面,包括化学品存储、危险品运输、生产过程安全管理、应急响应机制,对鲁西化工安全分享进行详细分析和阐述。通过深入探讨,希望能够引起读者的关注并为相关从业人员提供参考和启示。
正文:
化学品存储
化学品的储存是化工企业的基本操作,但不少化工企业在储存过程中存在一些问题,给员工和环境带来安全隐患。在鲁西化工的案例中,化学品储存是造成爆炸事故的原因之一。因此,企业要时刻保持储存设备的清洁和可靠性,保障储存环境的安全性,遵守化学品储存标准化管理和规范操作。
首先,企业应该加强监督管理,严格遵守国家有关安全生产法律法规,对储存设备进行定期检测和维护。其次,企业应该规范储存程序,对显性和隐性的化学品隔离、分类、标志、排列进行管理,并设置化学品同位分离区域,避免发生混淆、流失、泄漏的情况。最后,企业应该设立应急响应机制,建立员工应急培训、演练和演习机制,确保一旦发生事故能够及时处置和控制。
危险品运输
危险品运输过程中安全隐患也非常高,企业需要严格遵守国家危险品运输法规,并且在运输前对货物进行分类、封装和标识,保证货物运输的安全可靠性。在鲁西化工爆炸事故中,危险品运输是造成事故的主要原因之一。通过案例中的经验,我们可以总结出几个点:
首先,企业需要关注危险品运输路径,选择安全可靠的运输线路和交通工具。其次,企业需要规范危险品封装和标识,确保货物符合规范要求,降低运输过程中的风险。最后,企业需要对危险品运输过程进行监管和管理,确保车辆、司机和运输过程安全可靠,保证货物交付后及时清场并彻底清理。
生产过程安全管理
实际上,安全管理是化工企业生产过程中最关键的环节,企业应该强化安全文化建设,提高员工安全意识,严格执行生产操作标准,并优化安全管理流程。在鲁西化工爆炸事故中,企业在生产过程安全管理方面存在多个问题,导致事故爆发。
在安全管理方面,企业应该加强对员工的培训和监督。对于化工工人特别是新来的工人,企业应该对其进行安全操作培训,同时强制要求熟练掌握设备操作和应急处置,确保生产过程的高效运转和安全生产。另外,企业还需要强化制度、规章和标准,建立预防和探查隐患机制,及时了解生产过程中的安全隐患,并及时采取有效措施,消除安全隐患。
应急响应机制
在鲁西化工爆炸事故中,应急响应机制不足也是造成事故扩大的一个关键因素。企业在进行安全管理时,需要提前制定完善的应急预案,从预防、救助、抢险、查处和纠正几个方面进行细致安排和考虑。
首先,企业应该建立必要的应急物资储备,储备消防器材、抢险器材和急救药品等物资,确保及时应急。其次,企业应该制定应急预案,并定期进行演练,提高员工应急应变能力。最后,企业应该建立应急响应机制和安全管理评估机制,建立应急响应小组,对企业的安全状况和应急响应能力进行随时监控和管理。
结论:
鲁西化工的爆炸事故给我们带来了沉重的教训。化工企业必须加强安全管理,注重事前预防、事中处置和事后追溯,并保证相关政策规范的合规性。化工企业要时刻关注安全问题,深入挖掘隐患,进一步加强管理,以保证员工和环境的安全。同时,我们也需要在事故事后进行总结反思,不断提高自身的安全管理和应急响应能力。
此外,化工企业在进行危化品处置、危废处理、污泥减量处理、固废处理、土壤修复、化工清洗、化工设备回收等方面也应该注重安全,遵守国家有关法律法规、严格执行操作标准,确保安全生产。巴洛仕集团专业化工厂拆除和环保工程方面也需要注重安全,确保项目的顺利进行。
总之,这场事故再次提醒所有从业人员,在化学品存储、危险品运输、生产过程安全管理和应急响应机制等方面再次提高警惕,加强安全教育,提高安全防范意识,共同维护好企业生产和社会环境的稳定安全,共同推进化工企业全面、科学、规范、安全可靠的生产运行。
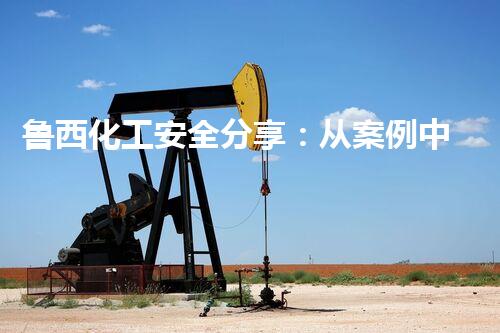